How a 'bionic' vest is boosting human abilities at a Ford plant
Mechanical EksoVest gives workers a lift to take strain off arms, boost their stamina
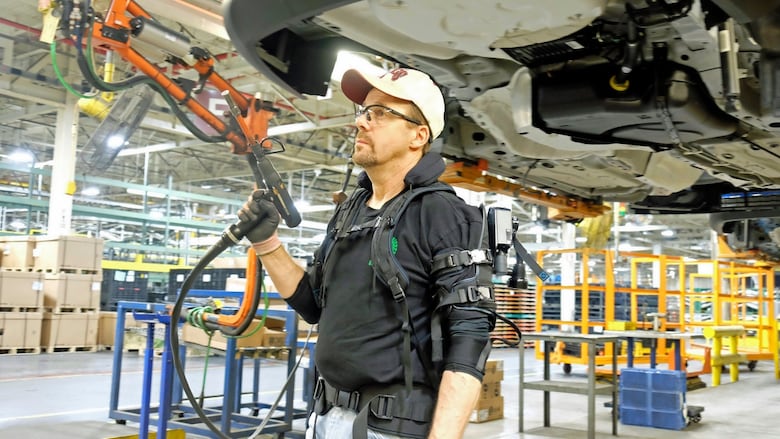
In theory, Paul Collins can do his entire job in 50 seconds. In reality, he has no choice.
That's how much time he has to work on the car suspended above him, before the next one takes its place — and he has to keep up that pace all day long. But lately he's had some help from what's best described as a "bionic vest."
Collins has been on the moving assembly line at Ford's Michigan plant for almost 24 years.
"It affected my life," Collins says. "My wife would say, 'honey, let's go do something' ... and she'd see me walk in the door and knew I was gonna tell her no. I was just too tired to do anything."
His job requires him to make very small changes to the vehicles that rumble by — a tweak here, a twist there. But being on the "high line," as it's called, means he is constantly raising and lowering his arms as he works on cars overhead.
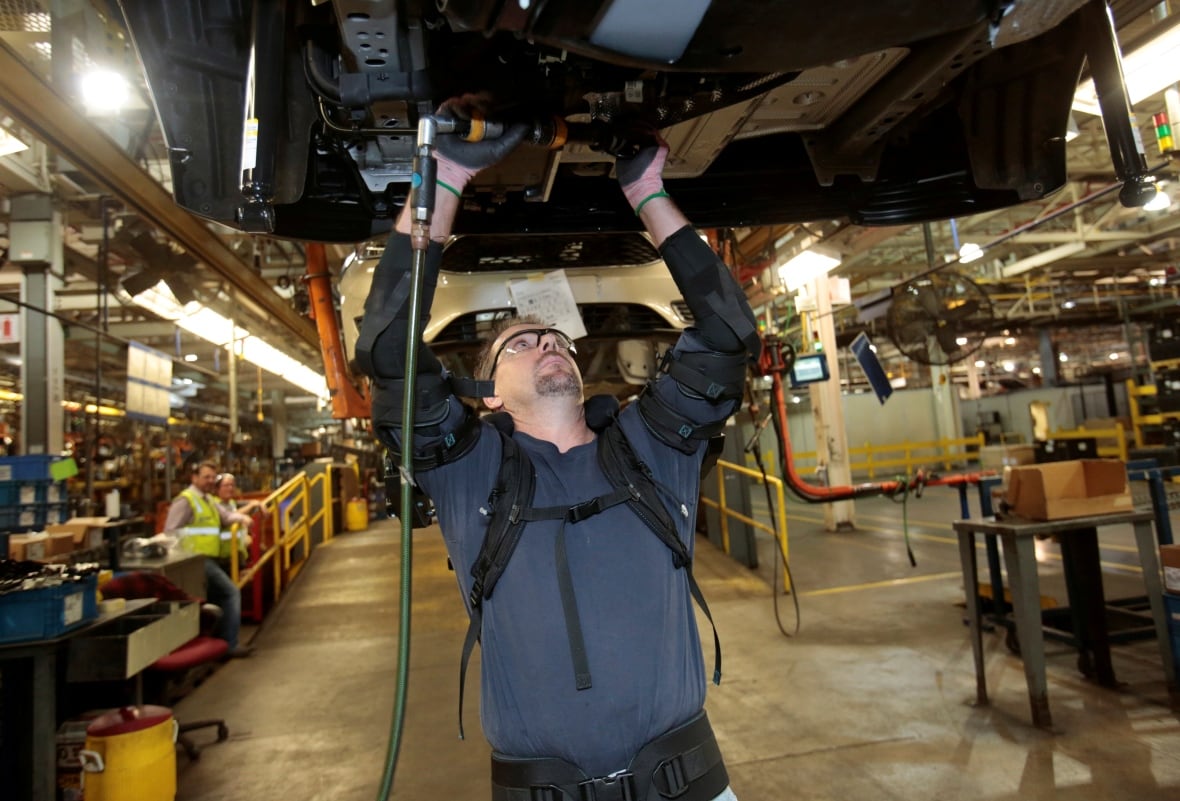
Try doing that five days a week, year-round, for decades.
"I was going home at night, flopping down on the couch, and I was Icy-Hotting my neck every single night," Collins says. "It's hard to explain pain, but you're tired, you're exhausted, you're fatigued."
The human shoulder is a wonderfully versatile and flexible joint — but it's also one of the weaker ones, and prone to injury.
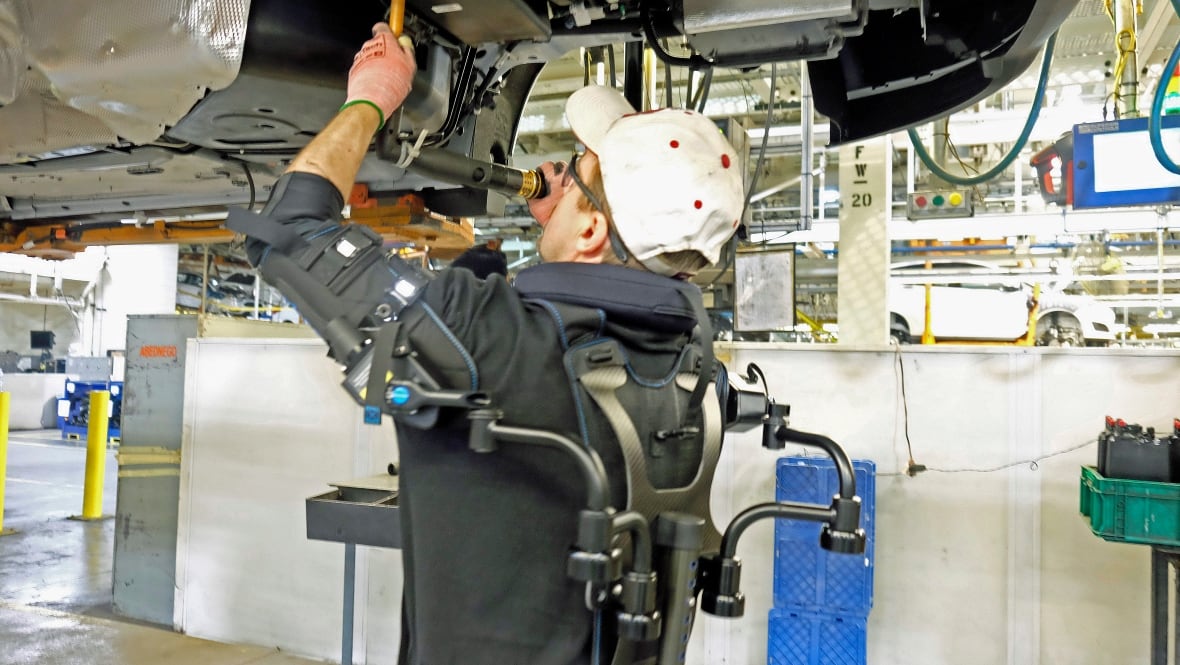
"The problem with the shoulder is once it's injured, it takes a long time to return to full functionality and it's very costly," says Marty Smets, the engineer at Ford who's taken charge of a pilot program to reduce workplace injuries.
"Depending on the length of time you're off work, it can be between $30,000 and $100,000 to repair a shoulder injury."
Augmenting humans
You might, at this point, ask: why do we still build cars by hand?
Humans, after all, have already largely been replaced in many factory jobs. Painting, for example, can be done almost entirely by machine.
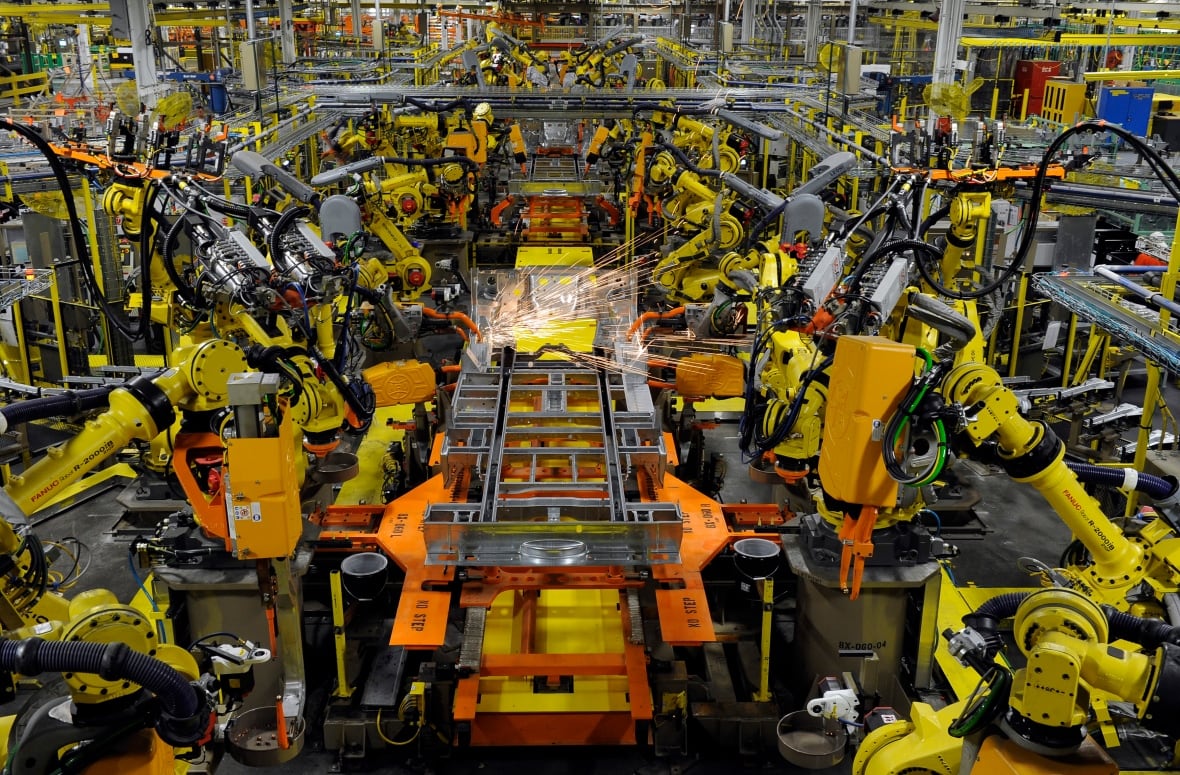
But jobs like those are exceptions to the rule; building vehicles is still very much a human-powered endeavour. In a complex work environment like a moving assembly line, machines notably lack intelligence, adaptability, and even precision.
So, Ford asked itself a question: if we can't yet give machines human-like intelligence, can we give humans machine-like stamina?
"Augmenting a human provides the best of both worlds," Smets says.
The 'bionic' vest
Ford has been offering a small number of its workers bionic vests for almost a year now as part of a pilot program.
The company makes it clear from the start: it's completely optional, and if employees don't want to wear one, they'll never have to. The union, for its part, has worked hard to get that in writing.
But you can see why a person might be curious.
The EksoVest, designed by Richmond, Calif.-based Ekso Bionics, doesn't give the wearer super-human strength. But giving each arm an additional 10 to 15 pounds of lift is enough to make a person's arms feel weightless — so all of a sudden, the prospect of working overhead all day isn't so tiring or hard on the body.
What also sets the vest apart is that it's completely mechanical. There's no cord, no battery, no electricity; it's powered by springs. They kick in gradually once the wearer raises their arms to about chest-height and beyond.
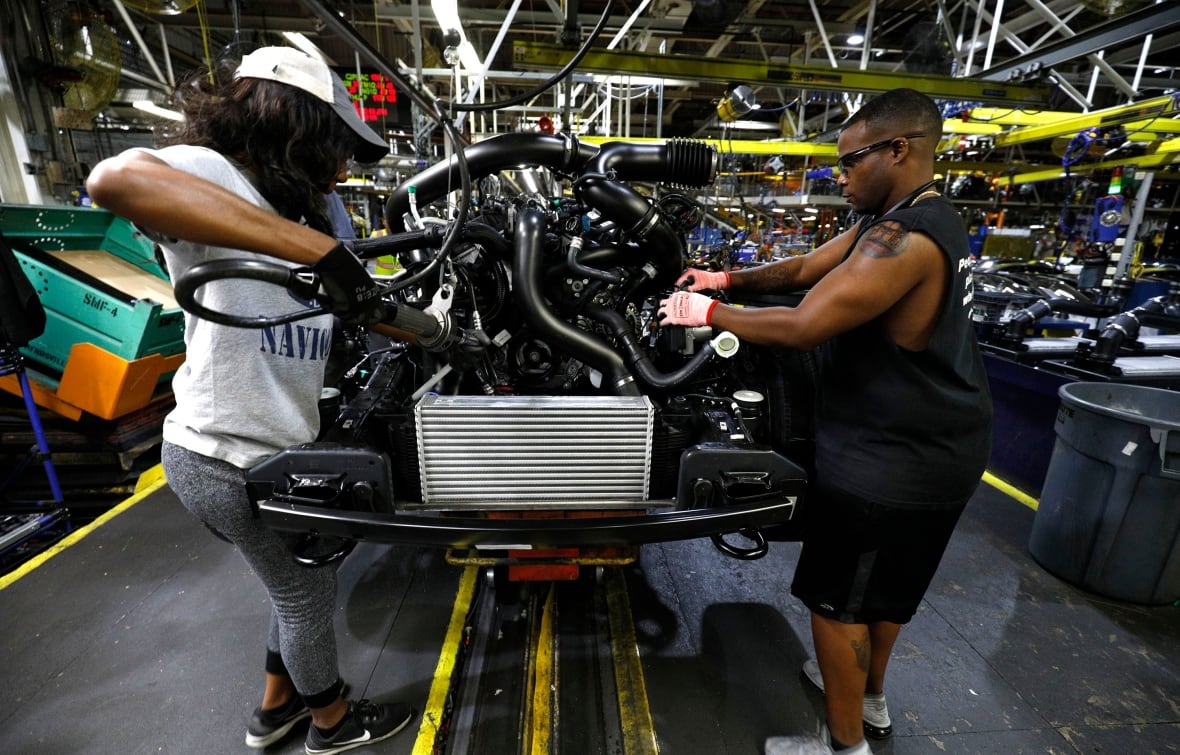
Paul Collins — "Woody" to his friends — remembers the first day he put it on.
"I've heard RoboWoody, RoboCop, I've heard Rocket Man," Collins says. "When I first had that thing on, they had a field day — you can imagine guys in the plant.
"[But] I'm not using any of my muscles at all — the vest is holding my arms — so instead of me exerting energy, the vest is doing that, taking all the pressure off my shoulder."
So how does he feel after a full day of working with the vest on?
"Aw, I feel fine. My neck — instead of having to Icy Hot it down three or four times like I told you earlier, I feel fine at the end of the day."
Cost vs. benefit
According to the manufacturer, a single vest sells for between $4,000 and $7,000 US.
But whether the company will save more than that in workers' compensation claims and health care costs is still an open question.
All of Ford's early data is quite deliberately anecdotal — after all, if workers don't like wearing it, the impact on the company's bottom line may not matter; a union uprising is in nobody's best interest.
But so far, the feedback has been positive. Collins, for example, doesn't want to give his trial vest back.
So Ford is now considering moving onto Phase 2, collecting actual empirical evidence that the vests are worth the cost. That means more trials on more people.
And according to Smets, there's no shortage of potential testers. Workers in Ford plants around the world — including from the company's assembly plant in Oakville, Ont. — have expressed interest.
And while this vest only provides lift assistance for a very specific range of motion — arms over your head, and not, for example, picking up something off the ground — the vest's manufacturer is already looking into ways to adapt the technology to other parts of the assembly line.
"It's best for chassis assembly … but in 10 years, we're gonna see these in a lot of places," says Ekso Bionics product manager Zach Haas. "Maybe painting can work too. Powertrain assembly is also possible."
The company has also developed similar suits for use in construction, and in physical rehabilitation.
But as for when we can expect exoskeletons to give us the super-strength required to lift entire cars overhead: don't hold your breath, says Haas.
"That's certainly more than five years away," he says. "More than 10, probably, to be able to lift your own body weight with minimal effort. More than 20 until we see real application in a plant."
Watch Andrew Chang's feature from The National on the EksoVest trials at Ford's Michigan assembly plant:
With files from Michael Drapack