Mining companies betting on autonomous technology to make dangerous jobs safer
Powerful tech allowing companies to remove human labour from underground work
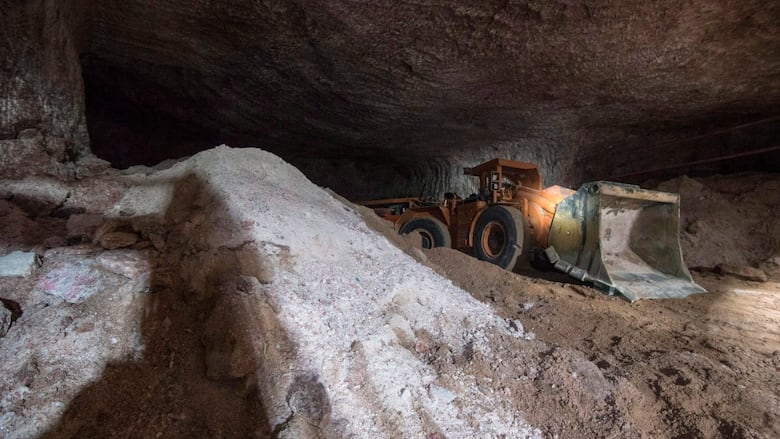
Forget about the canary in the coal mine — experts say the day is coming when there won't even be a need for a human.
The global mining industry has come a long way since the days when coal-blackened miners would carry a bird underground with them in hopes its distress would alert them to the presence of toxic gases.
Today, companies are employing everything from driverless haul trucks to remote-controlled and robotic drilling machines to remove human labour from some of their most hazardous operations.
Using a combination of radar, cameras, advanced sensing systems and cutting-edge technologies powered by artificial intelligence, Nutrien was able to operate one of its massive potash boring machines from a control room a few hundred metres away from the active mining face.
"It was just a huge success for us," said Shannon Rhynold, Nutrien's vice-president of potash engineering, technology and capital.
"Traditionally in potash mining, you've got these 250-tonne, massive pieces of equipment. There was always an operator sitting in the cab, running the joysticks, watching for various geological markers," she said. "One of the big challenges has been, 'how do you remove them from that machine'?"
The feat — the result of several years of intensive engineering work and experimentation — was a company first, with the goal of making potash mining safer by removing workers from the most hazardous underground locations.
"Let's be honest, when you've got a 250-tonne machine that's cutting into rock, there's noise, there's dust, there's heat, there's vibration," Rhynold said.
"And because you're opening that new ground, you're always at risk of what's in the ground above you, what's on the walls on the side of you."
Dangerous job
Mining has always been a dangerous occupation. The risks are most significant in underground operations, where workers face the possibility of everything from cave-ins and fires to floods and poisonous air.
But open-pit mines, too, contain potential hazards — including collisions and heavy equipment rollovers. Statistics from the Workers' Compensation Boards of Canada show there were 51 workplace fatalities in the mining, quarrying and oil and gas extraction industries in this country in 2021 alone.
That's why safety has been one of the main drivers behind an ongoing, massive transition toward automation in the industry, thanks to recent advances in AI and digital and remote technology.
At the Boddington gold mine in Western Australia, human drivers have been replaced by a fully autonomous haulage fleet of 36 trucks. In Chile, mining giant BHP is installing autonomous drills at its Spence copper mine. Chinese telecom firm Huawei has been installing 5G technology to allow underground mine workers to be replaced by machines operated from the surface.
Here in Canada, Teck Resources Ltd. is already using an autonomous haulage system at its Elkview steel-making coal mine in B.C.
"Automation is changing where a mine actually gets controlled — it doesn't have to be at the mine site," said W. Scott Dunbar, head of the mining engineering department at the University of British Columbia.
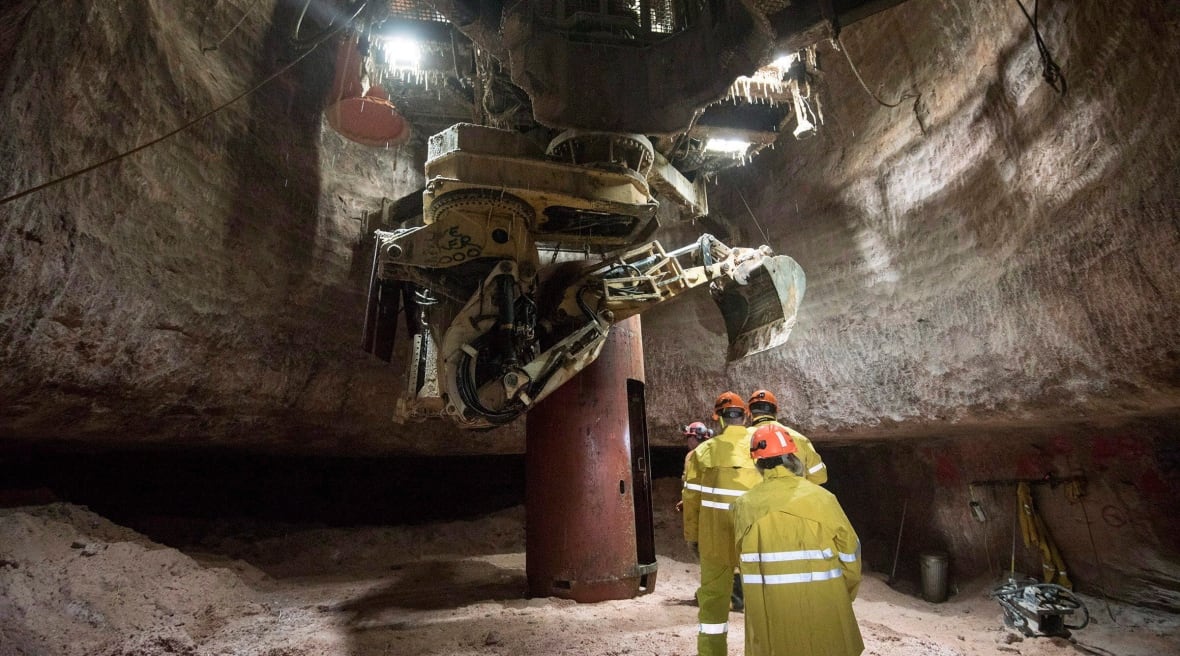
What about the jobs?
At an investor presentation earlier this year, Imperial Oil CEO Brad Corson said the company's fleet of autonomously operated heavy-haul Caterpillar trucks at its Kearl oilsands mine in northern Alberta is demonstrating 10 to 15 per cent higher productivity than staffed trucks.
"[An autonomous truck] can start reversing much, much more quickly than a staffed truck could do. And they can also pass by each other much more closely than you would ever allow with staffed trucks," Corson said. "So it really enables much faster loading."
The swift pace of automation is changing the types of jobs available at mine sites, in some cases making software skills more valuable at some companies than the ability to drive a truck.
Language in the current collective agreement between Teck Coal Ltd. and United Steelworkers Local 7884 — which contains an entire section about "technological change" and lays out the employer's obligations in the event that "mechanization or automation of duties" leads to job losses — illustrates the nervousness some employees may feel about the prospect of remote-operated equipment and driverless trucks.
But Nutrien says its tele-remote mining program has not eliminated any jobs at all — it's simply moved equipment operators from a hazardous physical location to a safe control room setting.
In fact, Rhynold said he believes remote and autonomous technology has the potential to make mining a more inclusive industry that is more attractive to women, older workers, the physically disabled and more.
"When you can work in an air-conditioned room, and here's the bathroom and here's the coffee maker and here's your nice ergonomic chair . . . I think that opens it up to much more diversity," he said.
"It potentially makes mining interesting to a wider range of people."
Mark Crouse, industry account executive for mining with software giant SAP, said he's been hearing mining customers talk about the potential for remote and autonomous technology for more than 20 years.
While the industry has only recently started moving more rapidly in this direction, Crouse said, he believes a day is coming when no one will have to go underground at all to mine the earth's resources.
"Remember how not that long ago people were using flip phones, and how quickly things shifted? It's not that far off," Crouse said.
"The capabilities are already there. The technology already exists."